Overcoming multiple challenges on a complex site, Keller used numerous techniques to boost Sydney Fish Market’s $750 million redevelopment.
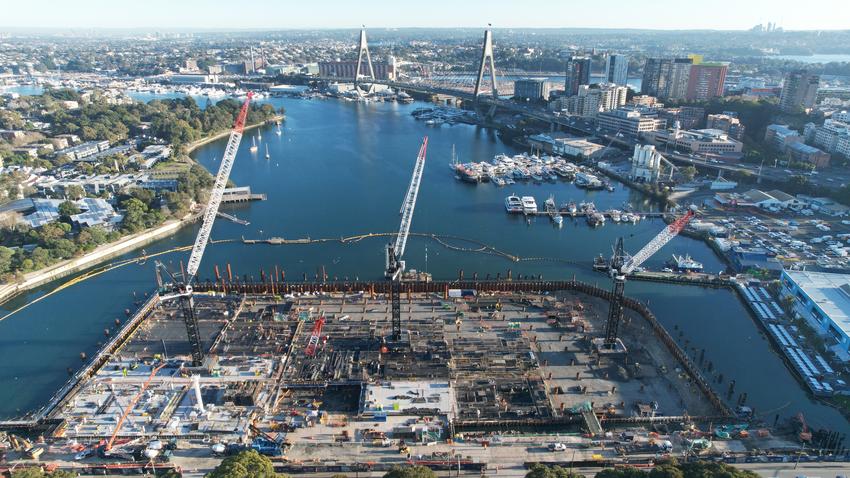
Sydney Fish Market is one of the city’s most popular tourist destinations and the lifeblood of Australia’s seafood industry, trading more than 50 tonnes and 100 different species of seafood every day.
Today the landmark is undergoing a massive transformation that will see operations move to a sleek new 35,000m2 complex at the head of Blackwattle Bay, creating a world-class waterfront destination with restaurants, promenade and welcoming public spaces. The project is proudly funded by the NSW Government.
With its design expertise, innovative approach to problem-solving and vast range of techniques, Keller has played a vital role in the project’s development over the past couple of years. Specifically, Keller was chosen by long-time client Multiplex to design and construct the land-side shoring wall for supporting the site’s basement car park – a project made more difficult due to a spatially and environmentally challenging site.
The right solution
“We’ve worked many times with Multiplex and they trust us to deliver, but one of the main reasons they selected us was because of our design expertise and combination of techniques compared to our competitors,” explains Gabriel Miler, Project Manager at Keller.
For example, while the original proposal called for the retaining wall to be built using cased bored piles, Keller recommended a combination of continuous flight auger (CFA) piles and jet grouting.
“The reason for this was multiple obstructions in the ground, including old concrete structures and steel beams,” he says. “CFA and jet grouting allowed us to work around them rather than spend valuable time trying to dig them out. In fact, once we got to site, there were even more obstructions than anticipated, so it proved to be the right decision and saved the project time.”
A small, congested site
Constructing the wall wasn’t just a challenge because of what was in the ground; the site itself is just a small strip of reclaimed land, barely 300m long and 8m wide, with Blackwattle Bay on one side and a main road on the other.
“It was an extremely congested area, requiring coordination with multiple other contractors and tight environmental controls to prevent spoils entering the water. Every movement or delivery had to be planned so we could all work together safely,” says Gabriel.
The wall itself needed to perform to the highest standard, with a deflection tolerance of less than 30mm next to the road and a water ingress of less than 10 litres a second. At the same time, it had to account for soft materials, seasonal and tidal movements, and an adjacent sheet pile wall.
All in the preparation
Before that work could start, however, Keller needed to tackle two other problems. The first involved turning the soft ground into a safe, stable working platform for the 100-tonne CFA rig. For this, the team stiffened the soils by treating 475m3 of earth with mass soil mixing. The other issue was the need to protect three culverts, which deal with storm water.. The solution here was to cover them with temporary concrete bridging structures, supported by a combination of CFA and micropiles.
Once the preliminary works were completed, the team was able to set about the main task of constructing the retaining wall, installing 147 CFA piles (900mm diameter) to depths of 12-23 metres, along with 122 jet grout columns (800mm diameter) and 48 ground anchors. Because there was no access from the water side, a specialised drill rig with a capability to drill under itself at 45 degrees was needed.
To finish off the project, the crew returned a few months later to install an additional 12 CFA piles to support the basement slabs of the new car park.
A proactive, partnership approach
“We had a lot of constraints on this project – not to mention some very wet weather at times,” says Gabriel.
“But I’m delighted that everything went well, and the client was happy with the way we handled everything. We partnered with them at every stage to proactively find a way forward and make their lives as easy as possible.
“The detailed planning before we even got to site really paid off and the constant communication when we were there showed how Keller can add value to even the biggest, most complex projects.”
Construction of the new Sydney Fish Market is due for completion in late 2024.